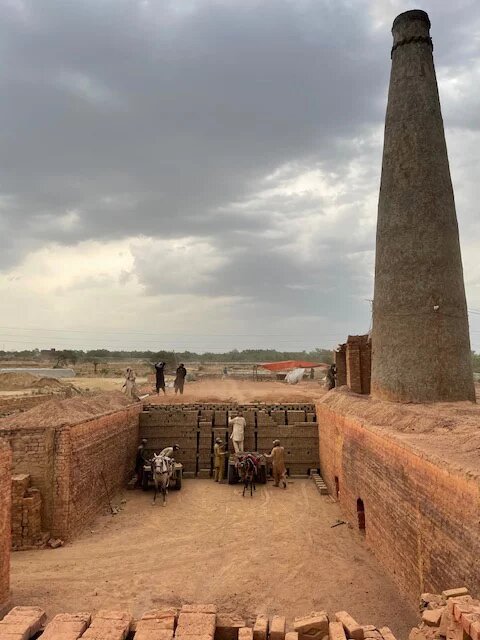
The conventional brick kilns of Pakistan are becoming more eco friendly with the introduction of a new technique of stacking bricks that burns less coal.
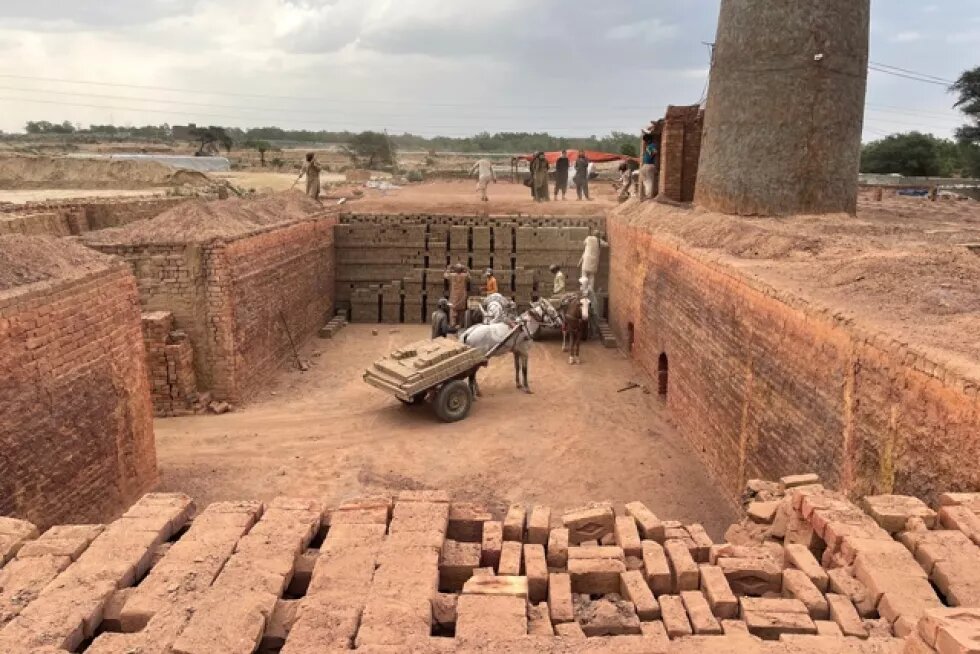
Smoke emitting brick kilns are found throughout rural Pakistan, dotting the landscape close to big cities and towns where a constant flow of bricks are needed for the construction of houses. Earlier, the commonly held view was that the blacker the smoke emitting from the chimney stack, the better the quality of the bricks being made inside the kiln. With the advent of zigzag technology used to transform conventional brick kilns into more eco friendly kilns since 2017, this “myth” has been shattered. Black smoke emitting from brick kilns is now accepted to be the result of poor combustion and inefficient burning of coal, which adds to choking air pollution in Pakistan’s cities and towns.
“The zigzag stacking technique uses less coal, spoons instead of spades and the coal is burnt efficiently emitting white smoke (from the vaporised moisture inside the bricks) instead of black smoke,” explained Asad Mahmood, the technical manager at the Government of Pakistan’s National Energy Efficiency and Conservation Authority (NEECA). “White smoke means the combustion process is optimised, hence there is no stream of un-burnt particles, which is good for the environment and also means more profits for the brick owners as they end up saving on coal.”
Bringing zigzag technology to Pakistan
NEECA along with the International Centre for Integrated Mountain Development (ICIMOD), an intergovernmental organisation working in the Himalayan-Hindu Kush region, provided the technical assistance to brick kilns’ owners in the Punjab to start converting their brick kilns to the more energy efficient zigzag technology in the past 2-3 years. This was supported by the Punjab Environmental Protection Department (EPD) and the Provincial Disaster Management Authority (PDMA), Punjab. In May, the Punjab EPD announced that conversion of almost all 8,000 brick kilns in the province to zigzag technology would reduce the air pollution by about 15 per cent.
Emissions from conventional brick kilns in Punjab, along with vehicular and other industrial emissions had contributed to the hazardous smog that blankets the province each winter season. A sectoral emission inventory of smog in Punjab conducted for a report prepared by the Food and Agricultural Organisation in 2019, showed that the major portion of total air pollutant emissions come from the transport sector which holds 43 per cent share, followed by 25 per cent from industrial sector (which includes emissions from brick kilns) and 20 per cent from agriculture. Converting brick kilns to zigzag was considered as a low hanging fruit for the Government of Pakistan. According to ICIMOD, which brought the technology to Pakistan, it reduces coal consumption by 20 per cent, carbon emissions by 40-60 per cent, produces more A-grade bricks, and brick production can be enhanced as well. A-grade bricks are of superior quality with greater strength and uniformity in colour.
Malik Amin Aslam, special assistant to the Prime Minister on climate change, said: “The incumbent government embraced zigzag technology-led brick kilns because it helps fight air pollution, save both public lives and the environment.”
Aslam, who played a vital role behind the shift, said that it was indeed a great milestone the Punjab government had achieved in such a short period of time to fight spiking air pollution in the province.
Training brick kiln owners
Mahmood, who led the trainings for the brick kiln owners from the government side, explained that there were many factors that contributed to this quick transition, starting off with the trainings of the initial few kiln owners onsite by ICIMOD and NEECA. He said: “The opportunity to network with brick kiln associations of other countries like lndia, Bangladesh and Nepal in the Federation of South Asian Brick Kilns Associations (FABKA) under ICIMOD also clarified the misconceptions related to zigzag kilns. The brick kiln owners felt that switching would be easy and there would be no requirements for a very high budget to retrofit the kilns. Subsequently, continuous technical support from NEECA and ICIMOD and facilitation from EPA and Ministry of Climate Change kept the ball rolling.”
According to him, the president of the All Pakistan Brick Kiln Association Shoaib Khan Niazi played a vital role after the success of the first zigzag kiln in Pakistan built in Lahore in 2017. “The first few kilns acted as a training centre for brick kiln owners in their respective districts without any government support. The extra profits, which brick kilns owners can earn from maximum production of A-grade bricks and money saved through less usage of coal per brick baked are the key driving forces for this transition,” Mahmood said.
EPA’s notifications and on ground actions by its teams were supported by the Punjab Disaster Management Authority (PDMA) and the local administration, which acted as a catalyst. In October, the administration in Khanewal district in South Punjab decided to demolish bricks kilns, which had not converted to zigzag technology as yet. Additional deputy commissioner (revenue) Muhammad Akram Malik said that such kilns were creating pollution in the environment and causing smog. He directed the assistant commissioners to visit all the brick kilns across the district to check on them and directed officers concerned not to purchase bricks from these kilns for development projects of the district government.
The government claims that 100 per cent of the brick kilns in Punjab have now been converted to zigzag. However, black smoke can still be seen emitting from many brick kilns in the province. “Let us just say that most of the brick kilns in Punjab have started their transition journey to zigzag. Some are at step 1, others have completed the entire process. It will take some more time,” explained Mahmood. “Many kilns may not be 100 per cent technically zigzag as only installation of blowers/ motors/ variable frequency drives cannot give us the required results until brick stacking and firing practices are changed.”
Fully functional zigzag kilns
To have fully functional zigzag kilns, the brick stacking pattern inside the kiln has to be changed. He explained further: “The name zigzag is basically attributed to the layout pattern in which the bricks are stacked. Then you need different techniques and training to feed coal, coal crushers from burning coal of uniform small size, its calorific value. One of the initial barriers, which kiln owners faced, was that once they trained their labour on the zigzag kiln they used to be picked up at high rates from other kiln owners, but once owners themselves managed the operations this issue was resolved to some extent.”
In zigzag kilns, bricks are arranged to allow hot air to travel in a zigzag path and this improves the heat transfer from the flue gases to the bricks, making the entire operation more efficient. In addition, better mixing of air and fuel allows complete combustion of coal, reducing coal consumption by about 20 per cent. The zigzag design also ensures uniform distribution of heat from the top down, improving the quality of the bricks.
According to Mahmood, the coal reduction potential is 2-3million tonnes per year roughly in the brick kiln industry in Pakistan and the decrease in coal consumption could be up to 50 per cent provided that high calorific value coal (good quality coal) is used and that zigzag kilns are operated in an efficient manner.
The traditional brick kilns in the country use mainly coal, rubber and shoe soles as fuel, emitting lethal back carbon emissions into the air. Most are located around urban areas and contribute significantly to air pollution. Given Punjab’s success, Aslam is now urging other provinces, where air pollution has become a leading cause of various health problems, to follow suit. The country's brick sector is highly unregulated but is responsible for around 1.5 per cent of the gross domestic product.
“We started our efforts in introducing zigzag technology in Pakistan back in 2017. Now with continuous government backing and support we have engaged most of the brick kilns in the Punjab to convert to this technique. One brick kiln can produce up to 20,000 bricks a day and with this technology their output has also gone up along with the quality of bricks, which are now 90 per cent A Grade quality. That’s a value addition of Rs.12 a brick (brick of inferior quality was Rs. 8 a brick). It makes business sense for the brick kiln owners to convert to zigzag. Besides, with commodity prices increasing across the globe, coal is becoming more expensive as well. This way they can save on coal costs as well,” he said.
According to him, other provinces like Khyber Pukhtunkwa have yet to follow suit, but brick kiln owners in the other provinces are already interested in converting their kilns and are getting in touch with trainers who are now experts in zigzag.
Black smoke means money wasted
Ghazanfar Ali is the president of the Brick Kiln Association of Islamabad/ Rawalpindi. Ali, who owns three brick kilns on the outskirts of Islamabad, converted to zigzag in early 2020 and has no regrets. He said: “I did this willingly before there was government pressure to do so. I use only high quality coal from Quetta and have made savings in costs and more than 20 per cent increase in profits. My bricks are of superior strength and quality and only white smoke comes out of my chimneys. Now brick kiln owners from nearby Khyber Pukhtunkwa province are approaching me and asking me for help in converting their kilns to zigzag!”
Workers skilled in zigzag technology are sought out by brick kiln owners and paid more than conventional brick kiln workers. “There is a constant demand for bricks in construction and the most important job in zigzag is that of the brick stacker. I pay my skilled stackers Rs.40,000 a month plus free food” explained Ali. The other labourers who feed the coal and make the raw clay bricks are paid Rs.25,000 per month plus free food. He said he had increased everyone’s salaries given the increased profits he was now making. Besides, if he did not increase their salaries they would be poached by other brick kiln owners keen to convert to zigzag.
His manager Altaf Hussein said: “We don’t take any bonded labour here. We hire from the local community and we pay them well. We also use the best quality coal from Quetta. For us black smoke emitting from the chimney means loss of money as we must be over feeding the coal. White smoke means that money is being saved on coal."
In his view, there is no alternative to coal use in brick kilns in Pakistan as yet. “Burning of coal makes the best and strongest bricks – we don’t know of any alternative fuel that works as well”.